Upcycling food waste into alt protein: On-site insect farming developed for manufacturers and retailers
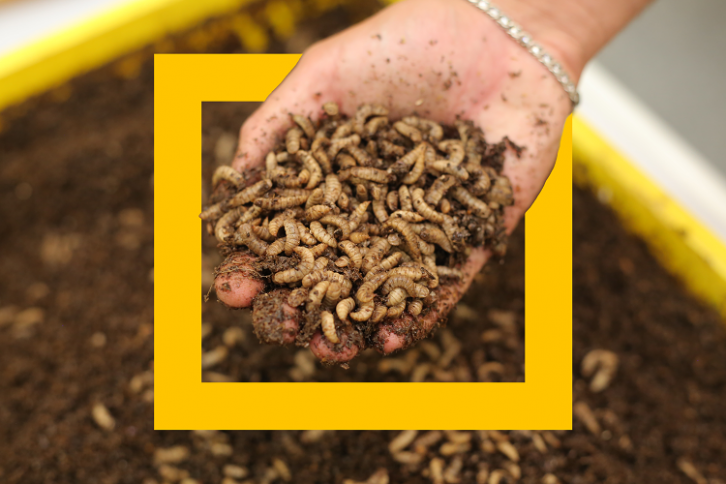
Far too much food intended for human consumption never reaches our plates. Globally, one-third of all food production is discarded annually, across the entire supply chain.
At the same time, the world is facing a protein shortage. According to the UN Food and Agriculture Organization (FAO), we’re predicted to be 60m tonnes short of protein per 2050. But continuing to rely on soy, a primary animal feed source, is not the solution, according to Larry Tadjo Kotch, co-founder and CCO of insect farming start-up Flybox.
Soy is known to be a leading driver of deforestation, and with 80% of the world’s soy produced in North and South America, it can be a ‘pricy import’, we were told. “Not only are food producers constantly faced with ecological challenges, but they are also confronted by economic difficulties in implementing the necessary sustainable practices.”
Kotch is adamant an alternative solution is ‘urgently’ needed. Together with CEO Andrea Jagodic and CFO Thomas Stringer, the trio has founded Flybox: a start-up developing insect farming technology for food businesses to upcycle organic waste on-side into a sustainable protein alternative for livestock, and frass fertiliser (a mixture of insect excrements, substrate, dead eggs etc.) for ‘healthier’ soils.
The ‘world’s first’ modular end-to-end insect farm
This year, Flybox built what it claims is the world’s first modular end-to-end insect farm to demonstrate how the technology can be deployed in any climate or country, thanks to its patent pending climate control technology. Flybox can even be used off-grid.
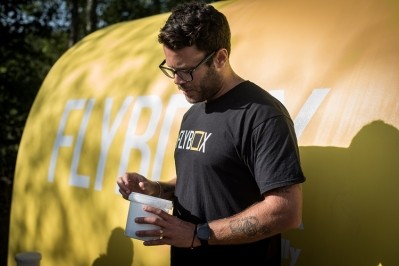
When a food business – ranging from farms to manufacturers and retailers – selects a Flybox product, the start-up manages its deployment. That being said, Flybox does not manage the day-to-day of the insect farming business. “Each Flybox product is automated to a great extent, and the customer is given software to monitor key information and metrics related to their operations at all times, but there is an element of labour required to operate a Flybox insect farm,” Kotch told FoodNavigator.
If a food business selects a ‘Starter Farm’, for example, its insects are delivered and if desired, Flybox will help with product ‘offtake’. But the customer will be responsible for loading in and mixing their waste into the ‘waste module’ and loading waste mix and larvae into the ‘grow module’. They are also responsible for removing and packaging it when the bioconversion process is done, the co-founder explained.
The start-up’s flagship model, the Flybox Grow, produced insect protein that agri-food companies can use to make animal feed. Results suggest the feed can lead to a 37% higher growth rate in fish, 30% increase in pig carcass weight.
The Flybox Grow can also make ‘frass’ fertiliser in the form of insect manure. Rich in food fibres, chitin, organic matter, insect skins, insect droppings and minerals, frass fertiliser can help reduce synthetic fertilizer use and improve the sustainability of farming operations.
Tests suggest using frass fertiliser instead of commercial organic fertilisers can increase yield by up to 65%.
Flybox’s default processes and technology are built for the Black Soldier Fly, which is the species used for around 80% of the insect market today. “That being said, you can grow a variety of insect species in a Flybox farm,” said Kotch.
Business opportunities and regulatory hurdles
Opportunity exists for supermarkets to onboard Flybox technology and upcycle the organic waste produced on site. It is estimated that in the UK alone, supermarket retailers throw around 100,000 tonnes of edible food per year.
So far, food retailers have responded ‘incredibly well’ to insect farming as a means of sustainably dealing with organic waste, Kotch told this publication. But one ‘hold up’ for retailers is decided what to do with the offtake: the alternative protein and frass fertiliser, amongst other products.
“That’s why Flybox supports partners who need offtake with an ecosystem ready for the products that waste bioconversion makes.”
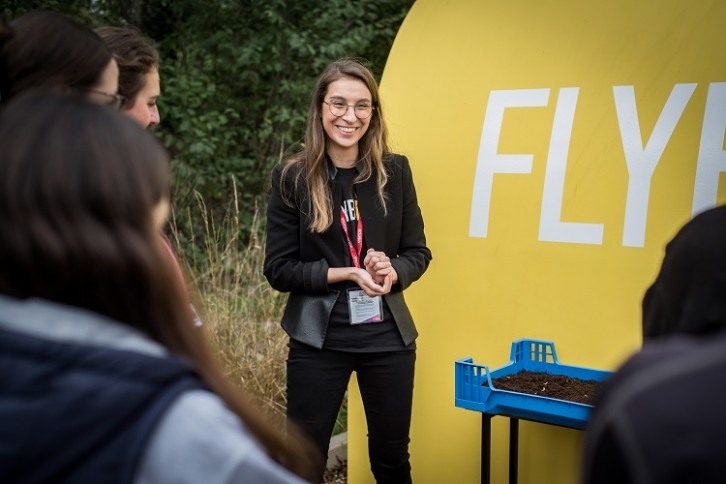
One potential hurdle Flybox has come up against is regulation, which is different in different territories. In most parts of Africa, for example, food waste and animal feed laws are flexible to feeding a vast range of waste substrates to insects, and then insects to livestock, said Kotch.
But in the UK, the use of insects in the certain parts of the food system, or the use of certain waste feedstocks as part of the insect rearing process, is prohibited. Europe is ‘far more advanced’ comparatively, we were told. “In order to see exponential change, the UK needs to adopt similar legislation, which is something we and a number of companies in the industry are working on.”
In the UK, only materials that contain products of non-animal origin (such as vegetal matter, residue from fruit and vegetable processing and brewery by-products and some products of animal origin such as milk, eggs and their products) can be used as a waste stream to feed insects. But this may change: Fera Science, based at the York Biotech Campus in the north of England, is conducting research commissioned by the Food Standards Agency (FSA), to examine whether waste streams could and should be expanded to include catering waste, mixed food waste, bakery waste and/or manure.
Small-scale insects for large-scale commercialisation
Having completed trials in partnership with Harper Adams University and Innovate UK over the summer, Flybox is now beginning to take on customers. Due diligence is being conducted, and productization strategies built, ahead of a planned 2024 deployment for five food businesses, the co-founder revealed.
“Alongside this, we have six sites currently operating between Nairobi, Kenya and Aylesbury, UK.”
Flybox’s ambition is to roll out its technology to 10 sites around the world next year. “Our main focus now is on customer experience: we are continuously drilling down unit economics, and qualifying customers to make sure they can benefit fully from insect farming and can scale fast.”
In the coming two to three years, Kotch told us we can expect ‘rapid scaling’ of the number of insect farms it deploys and an increased number of countries Flybox is deployed in.
“Longer term, we plan to expand our global footprint and become the largest vendor of modular insect farm tech. Our mission is build 1,000 insect farms by 2030.”