Nestlé invests £7 million into new hard-to-recycle plastics plant
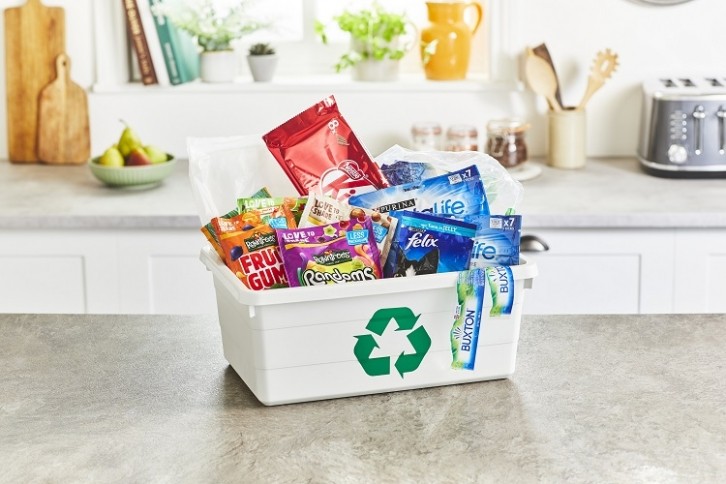
Overcoming the environmental implications of hard-to-recycle plastics and the barriers to handling them in food and beverage production is a key industry concern.
The problematic plastics category has spurred a new investment partnership between global giant Nestlé and technology company Impact Recycling. Eco-focused tech developer Impact Recycling has developed a breakthrough plastic recycling tech that will be at the centre of the company’s new UK recycling plant.
Nestlé is investing £7 million into Impact Recycling, which it hopes will advance how the food and beverage industry handles hard-to-recycle plastics in an environmentally responsible way. Along with a grant from Innovate UK, the plastics facility will be operational in late Summer 2024.
“We want to look for solutions where we can invest to stimulate the development of much-needed recycling infrastructure in the UK,” Sokhna Gueye, Head of Packaging at Nestlé UK and Ireland, told FoodNavigator.
The problems around plastic recycling
Plastics-focused plans, targets and advocates are gaining ground in the UK, spurring change in food and beverage operations. The UK government’s waste reduction strategy, the Plastics Pact and Innovate UK’s Circular Plastics Network seeks to eliminate the detrimental environmental impact of plastics.
Flexible plastic packaging makes up a quarter of the UK consumer packaging, yet only 8% was collected for recycling in 2022, for example, Ecosurety, a B Corp-certified UK compliance scheme, shared. In response, Nestlé stated it has undertaken extensive efforts to redesign its flexible packaging, transitioning from complex multi-material structures to simpler mono-material designs that are easier to recycle.
“Unfortunately, the current recycling infrastructure in the UK is not adequately equipped to handle these materials,” said Gueye. “This investment aims to address this pressing challenge and improve recycling capacity for flexible packaging,” added Gueye.
The UK’s Plastics Pact, launched by the Waste and Resources Action Programme (WRAP) charity, aims to address plastic waste’s impact on climate change. It aims to meet several targets: to eliminate problematic plastics, understand reusable versus recyclable packaging, increase plastics recycling to 70% and achieve 30% recycled content. The UK charity encourages more companies to engage in industry innovation and progress to achieve these targets.
Innovate UK’s Circular Plastics Network comprises a community of 5000-plus individuals who strive to progress plastic production, use and understanding to ensure they fit within a circular economy. One of its focus areas is its £60 million Smart Sustainable Plastic Packaging Challenge, which aims to support developments that can create positive change in the UK’s ability to tackle the 3Rs of plastic packaging waste: reduce, reuse and recycle.
A new way to recycle plastics
Impact Recycling will open its new plastic recycling facility in Durham, UK. The plant is designed to process hard-to-recycle flexible plastics typically used in food packaging. Its tech will turn these plastics into pellets that can be reused and repurposed into new flexible products such as postbags and refuse bags.
The tech works by separating post-consumer mixed rigid plastic waste to recover two consistent streams of post-consumer resin (PCR), polyethylene (PE) and polypropylene (PP), each containing a 98% purity.
A process called Baffled Oscillation Separation System (BOSS) organises the waste plastics by spinning them in water, which sorts different materials into those that sink and those that float, depending on their density. Separating plastic materials makes it easier to identify which ones can be recycled and enables businesses to implement the required measures to do so.
Speaking on Nestlé’s goals for the facility, Gueye shared: “When open, the facility will have the capacity to take 25,000 tonnes of flexible plastic, which means it has the potential to recycle more than the amount of flexible plastic packaging Nestlé UK and Ireland places on the market.”
Nestlé’s plastic goals
Plastics are a crucial element of Nestlé’s business operations. “It keeps our products safe and fresh on their journey to consumers, enables them to be transported and delivered safely, and offers information about the product itself,” Gueye said, commenting on understanding the critical role packaging plays at Nestlé.
“But we also recognise the urgent need to address the environmental impact of packaging waste, particularly plastics,” Gueye added. Nestlé has implemented a process to collect packaging, such as KitKat wrappers, Purina pet food pouches, Rowntree confectionery sharing bags and Nestlé Cereal bags from major supermarket collection points and onto recycling.
“Every action we take has an impact on making a difference to how packaging is recycled and giving it a second life,” Gueye said. “Supporting innovative technologies like Impact Recycling is just one of the many steps we are taking on our journey to ensure our packaging doesn’t end up as waste,” Gueye added.
Nestlé has adopted a five-pillar strategy across three main areas as part of its waste
reduction strategy. Firstly, it aims to create less packaging by reducing plastic or using virgin plastics. It also focuses on reuse and refill, Gueye said, rather than disposable packaging and strives to create better packaging by using alternative materials to facilitate recycling. In addition, it is working to develop better recycling systems and help to rethink behaviours internally and with partners and consumers.
“In the UK and Ireland, our efforts continue at pace to ensure as close to 100% of our packaging is designed for recycling by 2025, and we continue to work towards all of our packaging being recyclable or reusable,” said Gueye.